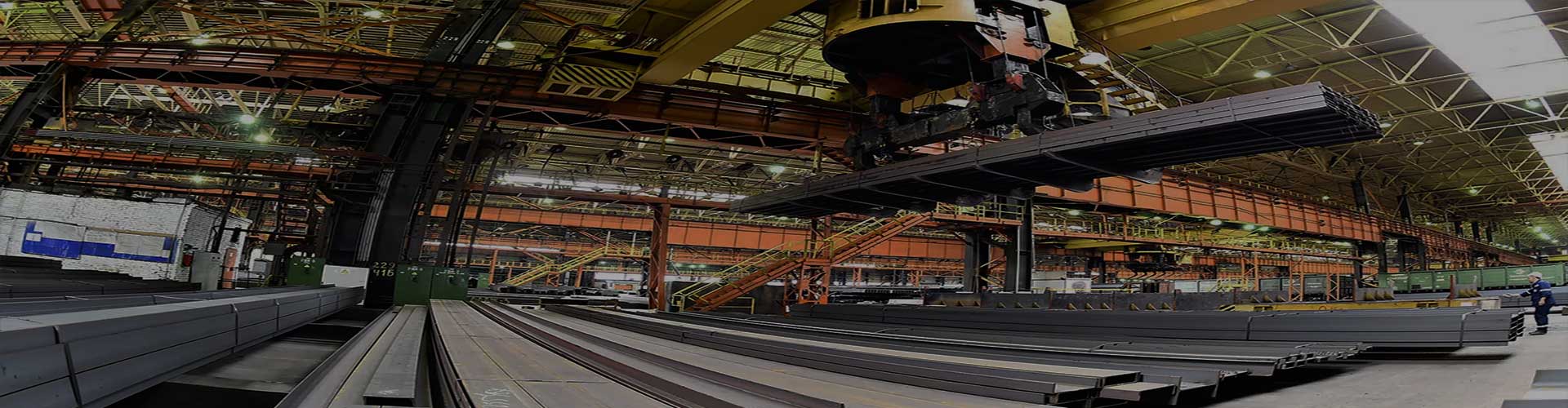
3000 Tons Press Heating Furnace
3000 Tons Press Heating Furnace
- Capacity: A 3000 Tons Press Heating Furnace is a type of industrial furnace capable of handling and heating up to 3000 tons of material. This furnace is commonly used in steel manufacturing, aluminum smelting, and other heavy-duty manufacturing applications.
- Heating Method: To generate heat, the furnace employs a heating method that typically involves the combustion of fossil fuels such as natural gas or oil. The heat is then transferred to the material being processed via a heat exchanger system or direct contact.
- Design: A 3000 Tons Press Heating Furnace is typically designed with a large steel or ceramic-lined chamber that can hold the material being processed. To ensure uniform heating throughout the material, the furnace may also be equipped with multiple burners or heating zones.
- Control system: The furnace has a sophisticated control system that allows operators to adjust the temperature, pressure, and other parameters to achieve the desired results. To prevent accidents, the system may also include safety features such as alarms and shut-off valves.
- Applications: The 3000 Tons Press Heating Furnace is commonly used in heavy-duty manufacturing applications such as forging, rolling, and extrusion. It is also used in the production of metal alloys, ceramics, and other high-temperature processing materials.
Description
A 3000-ton press heating furnace is a type of industrial machinery used in the metalworking industry to shape and mold metal parts through a process called forging. It consists of a large hydraulic press, which can exert a force of up to 3000 tons, and a heating furnace that heats the metal to a temperature high enough to make it malleable.
The furnace typically uses electric or gas heating elements to heat the metal to a temperature between 1800 and 2200 degrees Fahrenheit (1000 to 1200 degrees Celsius), depending on the type of metal being used. Once the metal is heated to the desired temperature, it is transferred to the press using tongs or other handling equipment.
The press applies a tremendous amount of force to the heated metal, causing it to deform and take on the desired shape. This process can be used to create a wide range of metal parts, including gears, axles, crankshafts, and connecting rods, among others.
In addition to the press and furnace, a 3000-ton press heating furnace may also include various other components such as a cooling system to quickly cool the metal after forging, a lubrication system to prevent sticking and damage to the press, and a computer control system to ensure precise and consistent operation.
Heating furnace structure:
- Heating Chamber: This is the main compartment in which the material or metal to be heated is placed. The chamber is typically lined with insulating materials such as firebrick or refractory materials to prevent heat loss.
- Burners: The burners are in charge of producing heat in the furnace. The fuel source, which could be gas, oil, or electricity, determines the type of burner used.
- Combustion Chamber: The combustion chamber is where the fuel is burned in order to generate heat. It is usually located beneath the heating chamber and is linked to the burners.
- Control System: The control system within the furnace regulates the temperature, pressure, and other process parameters. It is typically made up of sensors, controllers, and actuators that monitor and adjust the operation of the furnace.
- Exhaust System: The exhaust system removes the waste gases produced by the furnace during combustion. It typically includes a flue, chimney, and other components that aid in the safe venting of gases outside the facility.
- Support Structure: The heating furnace is held in place by the support structure, which prevents it from collapsing due to the high temperatures and weight of the materials being heated.
3000 Tons Press Heating Furnace: Working Principle Of Heating Furnace:
A 3000-ton press heating furnace is a type of industrial furnace used to heat materials to very high temperatures before they are processed in a hydraulic press. The working principle of a heating furnace involves using various types of fuels or electrical energy to generate heat which is then transferred to the material being processed.
The heating furnace is typically made up of a chamber or enclosure that houses the material to be heated. The enclosure is designed to retain the heat generated within it and prevent it from escaping into the surrounding environment. The furnace is also equipped with a heating system that can use different types of fuels, such as gas, oil, or coal, or electrical energy to generate heat.
When the furnace is turned on, the fuel or electrical energy is used to heat up the heating elements in the furnace. As the temperature inside the furnace rises, the material placed inside begins to absorb the heat, causing its temperature to increase as well. The temperature is monitored and controlled using thermocouples, which measure the temperature of the material being heated and send signals to the furnace control system to adjust the heating elements to maintain the desired temperature.
In the case of a 3000-ton press heating furnace, the high temperature achieved within the furnace is used to soften the material being processed, making it easier to work with and shape using the press. The material is typically heated to temperatures of several hundred degrees Celsius or even higher, depending on the specific material and the requirements of the process.
The heating furnace is designed to provide uniform heating and precise temperature control to ensure consistent quality and accuracy in the finished product. It is also equipped with safety features to prevent accidents and ensure worker safety during operation.
Overall, the 3000-ton press heating furnace is a critical piece of equipment in heavy-duty manufacturing applications, allowing for the production of large, complex metal components with high precision and accuracy.