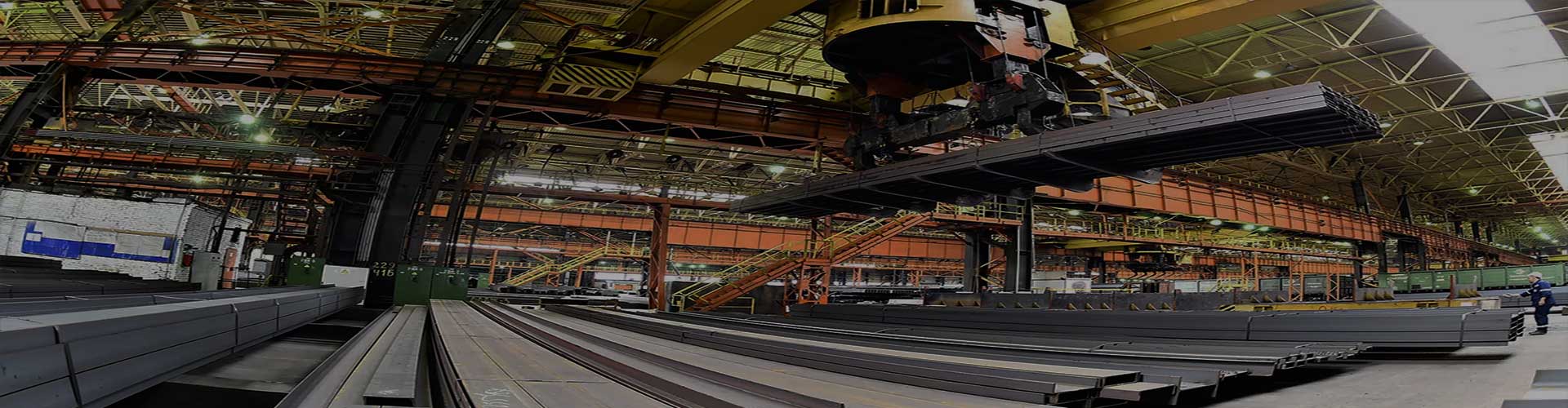
Continuous Forging Furnace
Continuous Forging Furnace
- Some of the common specifications of these furnaces include:
- Temperature range: Continuous forging furnaces can typically achieve temperatures between 900°C (1652°F) and 1300°C (2372°F) or higher, depending on the application.
- Heating method: The most common heating methods for continuous forging furnaces are gas-fired, electric resistance, or induction heating.
- Material handling system: A continuous forging furnace usually includes a conveyor system to move the metal through the furnace, ensuring a consistent temperature and heat treatment.
- Atmosphere control: Depending on the type of metal being heated, the furnace may need to be operated in a controlled atmosphere to prevent oxidation or other types of chemical reactions.
- Capacity: Continuous forging furnaces can vary in size and capacity, ranging from small batch-style furnaces to large, automated systems capable of processing large volumes of metal.
- Energy efficiency: Continuous forging furnaces may incorporate various energy-saving technologies such as recuperative burners or regenerative burners to increase fuel efficiency and reduce operating costs.
Description
A continuous forging furnace is a type of furnace used in the forging process for heating metal bars or other materials continuously, rather than heating them in batches. The furnace is designed to maintain a constant temperature, which allows for consistent heating of the material as it passes through the furnace.
The furnace typically consists of a long, narrow chamber, lined with heat-resistant material, such as refractory brick. The metal bars are fed into one end of the furnace and move through the chamber on a conveyor system or other mechanism while being heated to a specific temperature. The furnace may use a variety of heating methods, including gas-fired burners, electric heating elements, or induction heating. Some continuous forging furnaces also incorporate cooling systems to quickly cool the material after it has been forged, in order to prevent distortion or other defects.
Continuous forging furnaces are commonly used in the production of a wide range of forged components, including automotive and aerospace parts, hand tools, and machinery components. They offer advantages over batch-style furnaces, such as higher production rates, more consistent heating, and lower energy costs.
Product features: Continuous Forging Furnace
Continuous forging furnaces are specifically designed for high-temperature metalworking processes such as forging, extrusion and rolling. They offer several features that make them ideal for these applications. Here are some of the key features of a continuous forging furnace:
- Continuous Operation: As the name suggests, continuous forging furnaces operate continuously, allowing for a constant flow of workpieces through the furnace. This feature helps increase productivity and efficiency.
- Temperature Control: Continuous forging furnaces are designed to maintain a consistent and precise temperature throughout the heating zone. This ensures that the workpieces are heated uniformly and to the desired temperature.
- Energy Efficiency: Continuous forging furnaces are designed to minimize heat loss and maximize energy efficiency. They are equipped with insulation to reduce heat loss and are often designed with a regenerative burner system that recovers and reuses waste heat.
- High Throughput: Continuous forging furnaces are capable of handling large volumes of workpieces, making them ideal for high-volume production runs.
- Customizable: Continuous forging furnaces can be customized to meet the specific needs of different metalworking applications. They can be designed with multiple heating zones, different loading and unloading systems, and other features to optimize their performance.
Structure introduction:
The structure of a continuous forging furnace typically consists of the following components:
- Heating Zone: This is the section of the furnace where the metal workpieces are heated to the desired forging temperature. The heating zone can be divided into several zones with different temperature settings to achieve a precise temperature profile for the workpieces.
- Charging and Discharging System: The charging system of the furnace is responsible for feeding the metal workpieces into the heating zone. The discharging system is responsible for removing the heated workpieces from the furnace and transferring them to the forging press. Both systems are designed to operate continuously to maintain a consistent flow of workpieces through the furnace.
- Insulation: The furnace is lined with a layer of insulation to minimize heat loss and maintain the desired temperature within the heating zone.
- Control System: The furnace is equipped with a control system that monitors and regulates the temperature of the heating zone, the flow of workpieces through the furnace, and other key parameters to ensure consistent and reliable operation.
- Exhaust System: The furnace is equipped with an exhaust system to remove combustion gases and other byproducts of the heating process.
Overall, the continuous forging furnace is a complex system designed to heat metal workpieces to a precise temperature and maintain that temperature throughout the forging process, while also ensuring a continuous flow of workpieces through the furnace.