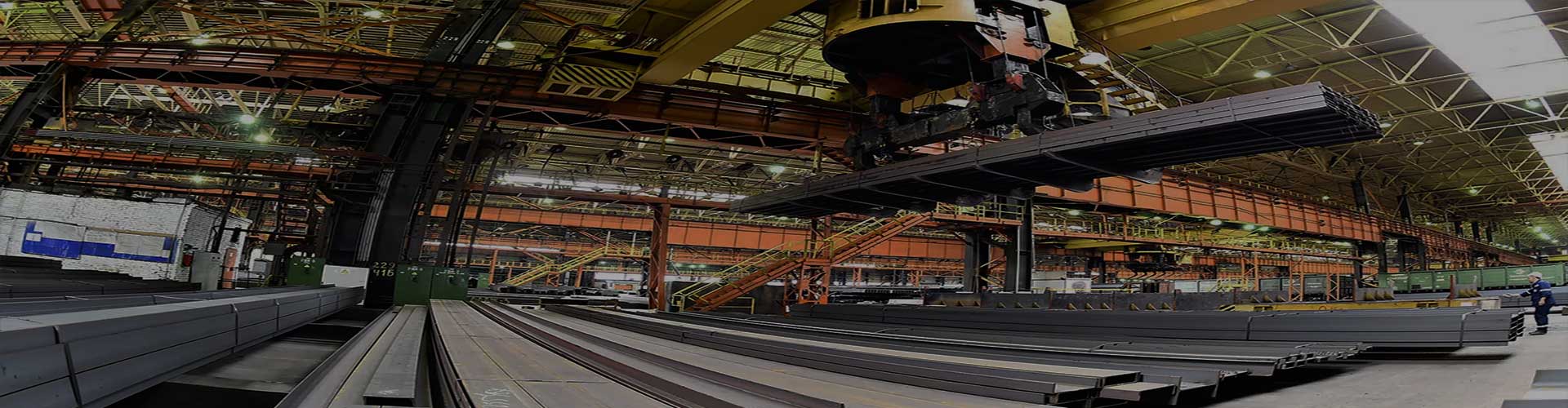
Regenerative Heating Furnace
Regenerative Heating Furnace
- Regenerative heating furnaces are becoming increasingly popular in both commercial and residential spaces due to their energy efficiency and low operational cost. The features of a regenerative heating furnace include:
- Regenerative Heat Exchange System: A regenerative heating furnace uses a heat exchange system that captures and stores waste heat from the exhaust gases and reuses it to preheat the incoming combustion air. This feature makes the furnace highly energy-efficient and reduces operating costs.
- High-Temperature Capability: Regenerative heating furnaces are capable of achieving high temperatures (up to 1800°C), which is necessary for heat treatment processes such as annealing, normalizing, and tempering.
- Precise Temperature Control: They use advanced temperature control systems to maintain precise temperature control throughout the heat treatment process. This feature ensures that the components are heated to the desired temperature, which is critical for achieving the desired mechanical properties.
- Uniform Heating: These furnaces provide uniform heating to the components being heat-treated, which ensures consistent quality and performance.
- Versatility: Furnaces are versatile and can be used for a wide range of heat treatment processes in various industries, including steel manufacturing, aluminum manufacturing, automotive industry, aerospace industry, and petrochemical industry.
Description
A regenerative heating furnace is a type of industrial furnace used for high-temperature heat treatment processes such as annealing, hardening, and tempering of metal components. The furnace operates on the principle of regenerative heat exchange, which involves capturing waste heat from the furnace exhaust gases and reusing it to preheat the incoming combustion air.
Structure:
The regenerative heating furnace consists of a combustion chamber, a regenerator, and a heat recovery system. The combustion chamber is where the fuel is burned to generate the heat required for the heat treatment process. The regenerator is a heat exchange system that allows the furnace to recover waste heat from exhaust gases and store it for reuse. The heat recovery system consists of ducts and valves that control the flow of hot gases and air through the regenerator.
During the heating cycle, the furnace operator sets the desired temperature and combustion rate. The combustion air is preheated by passing it through the regenerator, which absorbs heat from the hot exhaust gases. The preheated air is then fed into the combustion chamber, where it is mixed with the fuel and ignited to generate high-temperature heat.
During the cooling cycle, the hot exhaust gases are redirected through the regenerator, where they transfer heat to the refractory material. This process stores the heat, which is then used to preheat the incoming combustion air during the next heating cycle. The furnace operator can control the flow of the hot gases and air using the ducts and valves in the heat recovery system.
Regenerative heating furnaces are highly efficient and can achieve temperatures of up to 1,500°C. They are widely used in the manufacturing of steel, aluminum, and other metals where precise temperature control and energy efficiency are essential. Regenerative heating furnaces are also environmentally friendly as they reduce energy consumption and greenhouse gas emissions.
Scope of application: Regenerative Heating Furnace
Regenerative heating furnaces are suitable for a wide range of heat treatment processes in various industries, including:
- Steel Manufacturing: Regenerative heating furnaces are widely used in the steel industry for the heat treatment of steel products such as bars, billets, plates, and coils. They are used for processes such as annealing, normalizing, quenching, and tempering.
- Aluminum Manufacturing: Regenerative heating furnaces are also used in the aluminum industry for the heat treatment of aluminum products such as sheets, coils, and extrusions. They are used for processes such as solution annealing, aging, and stress relieving.
- Automotive Industry: Regenerative heating furnaces are used in the automotive industry for the heat treatment of components such as engine parts, gears, and bearings. These components require precise temperature control and uniform heating to achieve the desired mechanical properties.
Advantage:
Regenerative heating furnaces offer several advantages over traditional heating furnaces, including:
- Energy Efficiency: Regenerative heating furnaces are highly energy-efficient as they recover waste heat from the exhaust gases and reuse it to preheat the incoming combustion air. This process reduces fuel consumption and lowers operating costs.
- Uniform Heating: They provide uniform heating to the components being heat-treated, which ensures consistent quality and performance.
- Precise Temperature Control: They use advanced temperature control systems to maintain precise temperature control throughout the heat treatment process. This feature ensures that the components are heated to the desired temperature, which is critical for achieving the desired mechanical properties.
- Reduced Environmental Impact: They are environmentally friendly as they reduce greenhouse gas emissions and energy consumption.
- Higher Production Rates: They can achieve higher production rates due to their high-temperature capability and efficient heat recovery system. This feature reduces cycle times, increases throughput, and improves overall productivity.
Function: Regenerative Heating Furnace
The primary function of a regenerative heating furnace is to provide high-temperature heat treatment to metal components. The furnace operates on the principle of regenerative heat exchange, which involves capturing waste heat from the furnace exhaust gases and reusing it to preheat the incoming combustion air. This process makes the furnace highly energy-efficient and environmentally friendly.
The regenerative heating furnace achieves its function through the following processes:
- Combustion: The furnace burns fuel (such as natural gas or oil) to generate heat required for heat treatment process. The combustion process occurs in the combustion chamber, where the fuel mixes with the preheated combustion air and ignites to generate high-temperature heat.
- Heat Recovery: The furnace captures waste heat from the exhaust gases and reuses it to preheat the incoming combustion air. The heat recovery process occurs in the regenerator, which is a heat exchange system that stores the heat from the exhaust gases and releases it to the incoming air during the next heating cycle.
- Temperature Control: The furnace uses advanced temperature control systems to maintain precise temperature control throughout the heat treatment process. The temperature control system regulates the flow of fuel and air into the combustion chamber to maintain the desired temperature.
- Cooling: The furnace uses a cooling system to cool the components after the heat treatment process is complete. The cooling system may involve forced air or water cooling, depending on the specific heat treatment process.