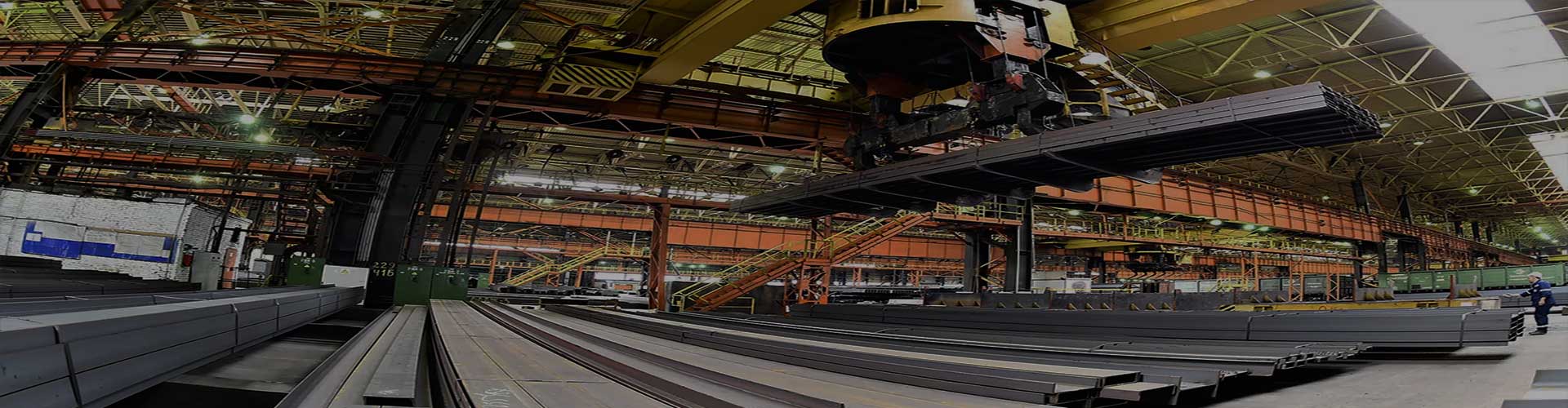
Heat Treatment Furnace
Heat Treatment Furnace
- Some of the key features of a Heat Treatment Furnace are:
- Temperature control: Heat treatment furnaces are designed to provide precise temperature control. The temperature can be set and controlled within a tight range to ensure that the desired heat treatment process is achieved.
- Heating elements: Heat treatment furnaces are equipped with heating elements that can generate high temperatures needed for heat treatment. The heating elements can be made of different materials such as ceramic, metal, or graphite, depending on the requirements of the heat treatment process.
- Insulation: Heat treatment furnaces are usually insulated to prevent heat loss and to maintain a uniform temperature inside the furnace. The insulation materials used can be ceramic fiber, refractory bricks, or a combination of both.
- Atmosphere control: Some heat treatment processes require specific atmospheric conditions such as inert gas or vacuum. Heat treatment furnaces can be equipped with an atmosphere control system to achieve the desired conditions.
- Cooling system: After the heating process is complete, the material needs to be cooled down to a specific temperature at a controlled rate. Heat treatment furnaces can be equipped with a cooling system such as water or air quenching to achieve the desired cooling rate.
Description
Heat Treatment Furnace is a type of industrial furnace used for heating materials at high temperatures to achieve a desired change in their physical or chemical properties. These furnaces are commonly used for a variety of heat treatment processes, including annealing, hardening, tempering, and stress relieving.
The heat treatment furnace typically consists of an insulated chamber or oven, heating elements, temperature controls, and a system for circulating air or other gases. The materials to be heated are placed inside the furnace and subjected to controlled heating, cooling, and holding cycles to achieve the desired changes in their properties.
Heat treatment furnaces are widely used in industries such as aerospace, automotive, and metallurgy for treating a variety of materials including metals, ceramics, and composites. The choice of furnace depends on the specific requirements of the material being treated, such as the desired temperature range, heating rate, cooling rate, and atmosphere.
These are important tools in the manufacturing process, as they allow for precise control over the temperature, atmosphere, and other parameters of the heat treatment process. This enables manufacturers to produce materials with consistent quality and properties, which is essential for many industrial applications.
Heat Treatment Furnace: Working Principle
The working principle of a Heat Treatment Furnace involves heating a material to a specific temperature and holding it at that temperature for a specified period of time to achieve the desired change in its physical or chemical properties. The process usually involves three stages: heating, holding, and cooling.
- Heating: The material is placed inside the furnace, and the heating elements are activated to increase the temperature inside the furnace. The heating elements can be located at the sides or bottom of the furnace, and they generate heat that is transferred to the material through convection or radiation.
- Holding: Once the material reaches the desired temperature, it is held at that temperature for a specific period of time to allow the heat to penetrate and cause the desired changes in the material’s properties. The holding time can vary depending on the material and the desired heat treatment process.
- Cooling: After the holding time is completed, the material is cooled down to a specific temperature at a controlled rate. The cooling rate can be achieved through various cooling methods such as air, water, or oil quenching. The cooling rate is critical for achieving the desired microstructure and properties of the material.
The Heat Treatment Furnace can be operated under different atmospheric conditions, depending on the desired heat treatment process. For example, some processes require a controlled atmosphere of inert gas, such as nitrogen or argon, to prevent oxidation and achieve the desired results.
Overall, Heat Treatment Furnaces are designed to provide precise temperature control, uniform heating, and cooling rates, and consistent results for a wide range of heat treatment processes.
The characteristics
The characteristics of a Heat Treatment Furnace can vary depending on the specific type of furnace and the requirements of the heat treatment process. However, some of the general characteristics of Heat Treatment Furnaces are:
- High-temperature capability: Heat Treatment Furnaces are designed to operate at high temperatures ranging from several hundred degrees Celsius to over 1000 degrees Celsius. This high-temperature capability allows them to perform a wide range of heat treatment processes on various materials.
- Precise temperature control: Heat Treatment Furnaces are equipped with temperature controllers that provide precise temperature control. This allows for tight temperature tolerances, which are necessary for achieving the desired microstructure and properties of the material being treated.
- Uniform heating: Heat Treatment Furnaces are designed to provide uniform heating throughout the chamber to ensure consistent results. This is achieved through various means such as convection, radiation, or a combination of both.
- Different atmosphere controls: Heat Treatment Furnaces can be designed to operate under various atmospheric conditions depending on the specific requirements of the heat treatment process. For example, some processes require a controlled atmosphere of inert gas, such as nitrogen or argon, to prevent oxidation and achieve the desired results.
- Different cooling options: Heat Treatment Furnaces can be designed to provide different cooling options such as air, water, or oil quenching to achieve the desired cooling rate. The cooling rate is critical for achieving the desired microstructure and properties of the material.
Heat Treatment Furnaces structure
Heat Treatment Furnaces are generally made up of a few basic components that work together to create a controlled environment for heat treatment processes. The specific structure of a Heat Treatment Furnace can vary depending on the type and size of the furnace, as well as the specific requirements of the heat treatment process. However, some common components of a Heat Treatment Furnace include:
- Furnace shell: The furnace shell is the outer structure of the furnace and is typically made of a steel or other high-temperature-resistant material. The shell provides insulation and helps to contain the heat and atmosphere within the furnace.
- Heating elements: The heating elements are responsible for generating the heat required for the heat treatment process. The heating elements can be located at the sides or bottom of the furnace and are typically made of ceramic, metal, or graphite materials.
- Insulation: The insulation is used to prevent heat loss from the furnace and maintain a uniform temperature inside the furnace. The insulation materials can be ceramic fiber, refractory bricks, or a combination of both.
- Temperature control system: The temperature control system is used to monitor and adjust the temperature inside the furnace. The system typically includes a thermocouple or other temperature sensor, a temperature controller, and heating element power control devices.
- Atmosphere control system: Some heat treatment processes require a specific atmosphere within the furnace, such as a vacuum or inert gas. An atmosphere control system can be used to create and maintain the desired atmosphere inside the furnace.