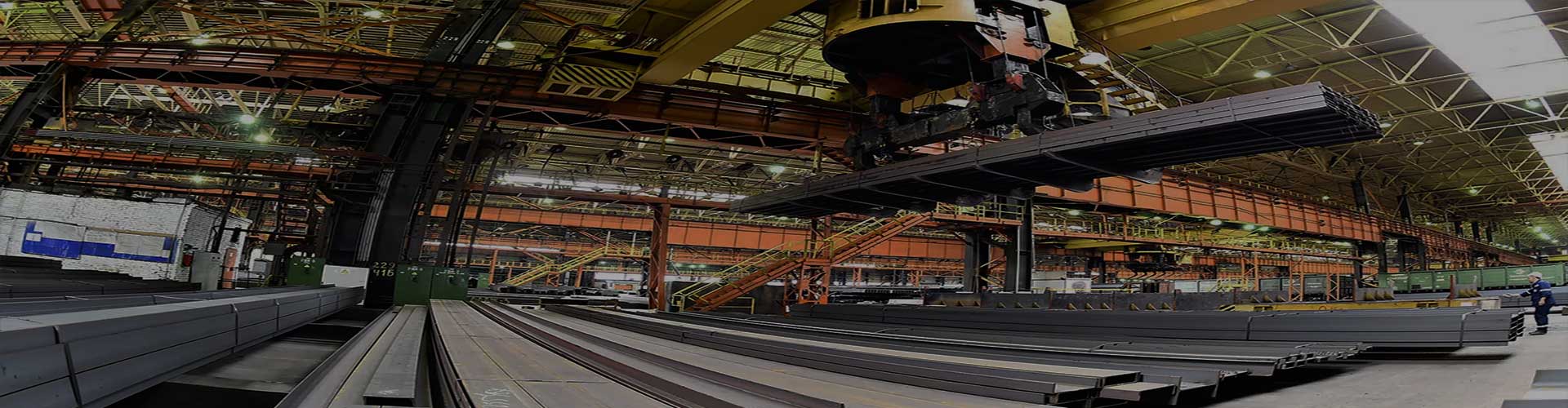
Rolling Mill Heating Furnace
Rolling Mill Heating Furnace
- The rolling mill heating furnace includes additional features, such as:
- Automatic charging systems: The furnace is equipped with automatic charging systems to load the metal products onto the furnace conveyor, reducing the need for manual labor.
- High-velocity burners: The furnace is equipped with high-velocity burners to improve heat transfer efficiency and reduce fuel consumption.
- Advanced control systems: The furnace is also equipped with advanced control systems that use real-time data to optimize the furnace operation, improve product quality, and reduce energy consumption.
- Fuel type: The furnace may be fueled by natural gas, propane, electricity, or other fuels, depending on the specific requirements of the production facility.
Description
A rolling mill heating furnace is a type of industrial furnace used in the metalworking industry to heat metal products before processing them in a rolling mill. The furnace is designed to heat the metal to a specific temperature, which is critical for achieving the desired properties and dimensions of the final product.
The rolling mill heating furnace is typically fueled by natural gas, propane, or electricity, and is designed to provide uniform heating of the metal product. The furnace may include temperature sensors and control systems to ensure that the metal is heated to the correct temperature, and may also include automatic charging systems to load the metal onto the furnace conveyor.
Once the metal product has been heated to the desired temperature, it is fed into the rolling mill, where a series of rollers apply pressure and shape the metal to the desired dimensions. The rolling mill heating furnace is an important part of the metalworking process, as it ensures that the metal is heated to the correct temperature and provides the necessary heat for shaping and forming the final product.
Working principle: rolling mill heating furnace
The working principle of a rolling mill heating furnace is to heat the metal product to a specific temperature before processing it in a rolling mill. The furnace is typically fueled by natural gas, propane, or electricity, and is designed to provide uniform heating of the metal product.
The metal product is placed on a conveyor and fed into the furnace, where it is heated to the desired temperature. The temperature inside the furnace is carefully controlled using a variety of temperature sensors and control systems to ensure that the metal is heated to the correct temperature. The furnace may also include automatic charging systems to load the metal onto the conveyor, reducing the need for manual labor.
Once the metal product has been heated to the desired temperature, it is fed into the rolling mill, where a series of rollers apply pressure and shape the metal to the desired dimensions. The rollers are typically arranged in pairs, with each pair of rollers applying pressure to the metal from opposite directions.
The rolling mill heating furnace may also include additional features such as high-velocity burners to improve heat transfer efficiency and reduce fuel consumption, and advanced control systems that use real-time data to optimize furnace operation, improve product quality, and reduce energy consumption.
The Characteristics
The characteristics of a rolling mill heating furnace may include:
- High accuracy and consistency: The furnace is designed to achieve and maintain the desired temperature range with high accuracy and consistency, which is critical for achieving the desired properties and dimensions of the final product.
- Uniform heating: The furnace provides uniform heating of the metal product, which helps to ensure that the product is heated to the correct temperature throughout.
- Efficient heating: The furnace is designed to provide efficient heating of the metal product, which can help to reduce fuel consumption and improve energy efficiency.
- Advanced control systems: The furnace may be equipped with advanced control systems that use real-time data to optimize furnace operation, improve product quality, and reduce energy consumption.
- Automatic charging systems: The furnace may include automatic charging systems to load the metal product onto the furnace conveyor, reducing the need for manual labor.
- High-velocity burners: The furnace may be equipped with high-velocity burners to improve heat transfer efficiency and reduce fuel consumption.