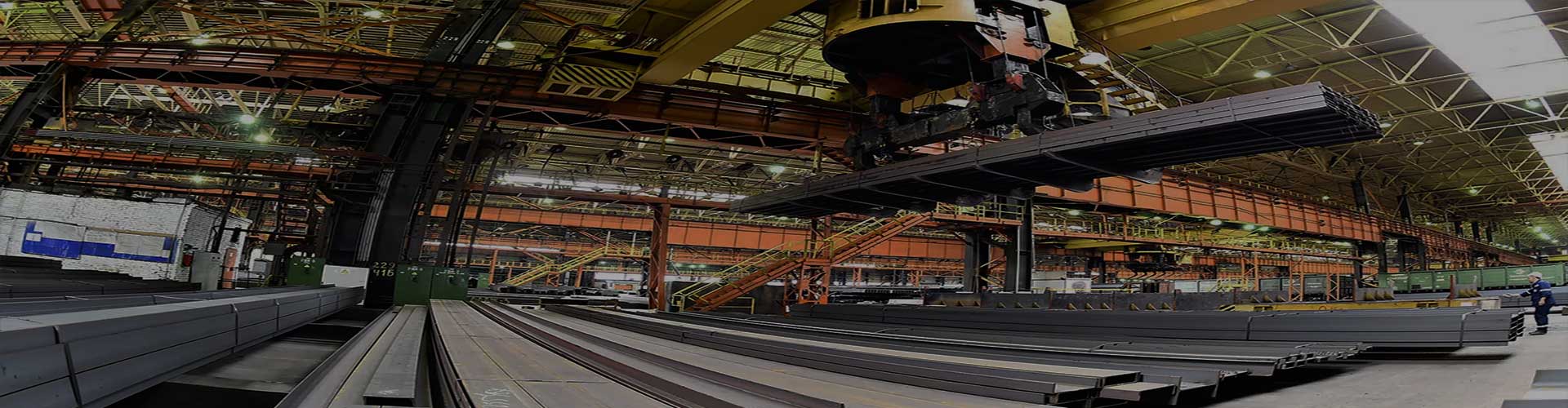
Walking Beam Furnace Mechanism
Walking Beam Furnace Mechanism
- Here are some common specifications for a typical walking beam furnace:
- Temperature range: The furnace can typically reach temperatures of up to 1300°C (2372°F) for some heat treating processes.
- Capacity: The walking beam furnace is capable of handling long workpieces such as bars, tubes, and structural shapes with a length of up to 60 feet or more.
- Heating system: The furnace uses a gas-fired heating system with burners located along the length of the chamber.
- Control system: The walking beam furnace is equipped with advanced control systems that optimize fuel consumption and reduce emissions.
- Walking beam mechanism: The walking beam mechanism consists of a series of reciprocating beams that support the workpiece and move it along the length of the furnace. The upper set of beams is fixed to a hydraulic cylinder or motor, and the lower set of beams is connected to the workpiece.
- Material handling: The furnace may be equipped with automatic material handling systems, such as conveyors or cranes, to load and unload the workpieces.
- Energy efficiency: The walking beam furnace is designed to be energy efficient, with high thermal efficiency and low emissions.
- Safety features: The walking beam furnace is equipped with safety features, such as temperature sensors, interlocks, and alarms, to ensure safe operation and prevent accidents.
Description
A walking beam furnace is a type of industrial furnace used for heat treating processes such as annealing, normalizing, and hardening of steel. It is designed to move the workpiece through the furnace using a walking beam mechanism, which consists of a series of reciprocating beams that support the workpiece and move it along the length of the furnace.
The walking beam furnace is ideal for heat treating long workpieces such as bars, tubes, and structural shapes, as the walking beam mechanism allows the workpiece to move continuously through the furnace without the need for manual handling. This results in a more uniform heat treatment process and can increase production efficiency.
Walking beam furnace: working principle
The working principle of the walking beam furnace is as follows:
- Loading: The workpiece is loaded onto the lower set of beams at the entrance of the furnace.
- Heating: The furnace is heated to the desired temperature using burners located along the length of the chamber.
- Walking beam mechanism: The walking beam mechanism consists of a series of reciprocating beams that move the workpiece through the furnace. The upper set of beams is fixed to a hydraulic cylinder or motor, which causes the beams to move up and down in a reciprocating motion. The lower set of beams is connected to the workpiece and moves with it as it is transported through the furnace.
- Transport: As the upper set of beams moves down, they push against the lower set of beams and cause the workpiece to move forward through the furnace. Once the upper set of beams reaches the end of its stroke, it moves back up, and the lower set of beams continues to move the workpiece forward.
- Unloading: The workpiece is unloaded from the walking beam furnace at the exit end.
The characteristics: Walking Beam Furnace Mechanism
The walking beam furnace has several key characteristics that make it well-suited for heat treating long workpieces:
- Continuous processing: The walking beam mechanism allows the workpiece to move continuously through the furnace without the need for manual handling, resulting in a more efficient and uniform heat treatment process.
- High temperature capability: The furnace can reach high temperatures of up to 1300°C (2372°F) for some heat treating processes, making it suitable for a wide range of applications.
- Large capacity: The walking beam furnace is capable of handling long workpieces such as bars, tubes, and structural shapes, making it ideal for industrial applications.
- Uniform heating: The burners located along the length of the furnace provide uniform heating, ensuring that the workpiece is heated evenly throughout the process.
- Energy efficiency: The walking beam furnace is designed to be energy efficient, with advanced control systems that optimize fuel consumption and reduce emissions.
Technical Parameters
Name | Technical parameters |
Description | Walking beam type copper/brass slab heater |
Material | Copper, brass,cupro-nickel alloy etc |
Slab size | Thickness 160mm160mm
Width 400~420mm400~420mm Length 3000~4600mm3000~4600mm Standard Max. weight: 2.75t/piece/(160×420×4600mm) 2.75t/(160×420×4600mm) |
Heating capacity | Minium 12t/h, 4slab/h(1slab:160×420×4600mm)
:12t/h 4/h(160×420×4600mm) |
Heating temperature | 730~750ºC±5ºC(max 850ºC) |
Hearth temperature() | 800~900ºC |
Fuel | Natural gas LNG |
Heat value | 8900Kcal/ Nm3 |
Air preheating temperature | 250~450ºC |
Heat efficiency of the furnace | ≥45% |
Thermal control pattern | Auto/ manual, impulse, remote control, |
Burner type | Imported flat flame burners of Germany KROM schroder.
heating zone each burner:23 Nm3/h;soaking zone each burner:15 Nm3/h KROM schroder.23 Nm3/h;15Nm3/h |
Number of burners | Total: 18 PCS, heating zone:8PCS,
Soaking zone: 10 PCS 18,8,10 |
Rated burning capacity | Max:334 Nm3/h
:334 Nm3/h |
Dimension of the hearth | W5000×H1200×L8000mm
5000×1200×8000mm |
Loading capacity | 16slabs/batch×2.75t/piece=44t/batch
16/×2.75t/=44t/ |
Total length of furnace | ~11m
~11 |
Loading and unloading method | End feeding and side discharge |
Loading pattern | Single row,3 zones, preheating zone2.5m, heating
zone 3.5m, soaking zone 2m ,, 2.5m,3.5m,2.0m |
Vertical movement of walking beams: | Lifting: 90mm, 90mm
Lowering: 80mm 80mm |
Horizontal travel of walking beams: | 500mm |
Heat interchanger | Hot tubular exchanger |
Heated up time | ~4 hours
~4 |
Quantity of heated up zone | 3 zones 4sections
34 |
Material and space | Slab: W420mm; slab in furnace:16pcs;
Gap between slab and slab: 80mm; Stroke: 500mm 420mm;16;80mm;500mm |
* Walking Beam Type Slab Heater Technical Data
Parts Name | Parameters | Guarantee value &precision value |
Remarks | |
Production quality |
Slab tapping temperature contrast | ±5ºC | ||
Slab full-length curvature | ≤5mm/m | |||
Surface quality | No scratches, , |
|||
Loading Device |
Loading speed | 7.5min/time 7.5min/ |
||
Storing materials | ≥3 PCS | |||
Length measuring bias | ±5mm | |||
Width measuring bias | ±3mm | |||
Charging positioning accuracy | ±5mm | |||
Travel route measuring | ±5mm | |||
Combustion system | Hearth pressure control accuracy | ±10Pa ±10Pa |
||
Furnace temperature control accuracy | ±5ºC | |||
Furnace atmosphere control accuracy |
Micro-oxidizing | O2≤2% | ||
Micro- reducibility | CO:0~1% | |||
Burner Life | ≥3 years | |||
Walking beam Device |
Total running deviation(cold) () |
±20mm | ||
Total running deviation(hot) () |
±30mm | |||
One walking beam precision | ±1.5mm | |||
Furnace shell | Furnace wall temperature | Max 45ºC | ||
Fiber refractory lining life | ≥5 years | |||
Bottom furnace refractory life | ≥5 years | |||
Unloading device | Furnace door opening-close time | 7.5min/time | ||
Heat exchanger |
Air preheating temperature | ≥300ºC | ||
Heat exchanger life | ≥3 years | |||
Exchanger | flue gas exit temperature | ≤450ºC | ||
Cooling water | Water seal yielding water temperature | Max 60ºC | ||
Others | Furnace output | ≥ 12t/h | ||
Sound from 1m from operating point 1 |
≤85db | |||
Furnace thermal efficiency | ≥45% |
* Energy and Media Consumption:
Item | Consumption value | Remarks |
Natural gas | 350Nm3/h | Heat value: 8900Kcal/Nm3
8900Kcal/Nm3 |
Cycle water | 12m3/h | |
Soft water | 4 m3/h | |
Electric | 5KWh/t | |
Nitrogen | 12 Nm3/time | |
12 Nm3/ | ||
Compressed air | 0.2 Nm3/time | |
0.2 Nm3/ |