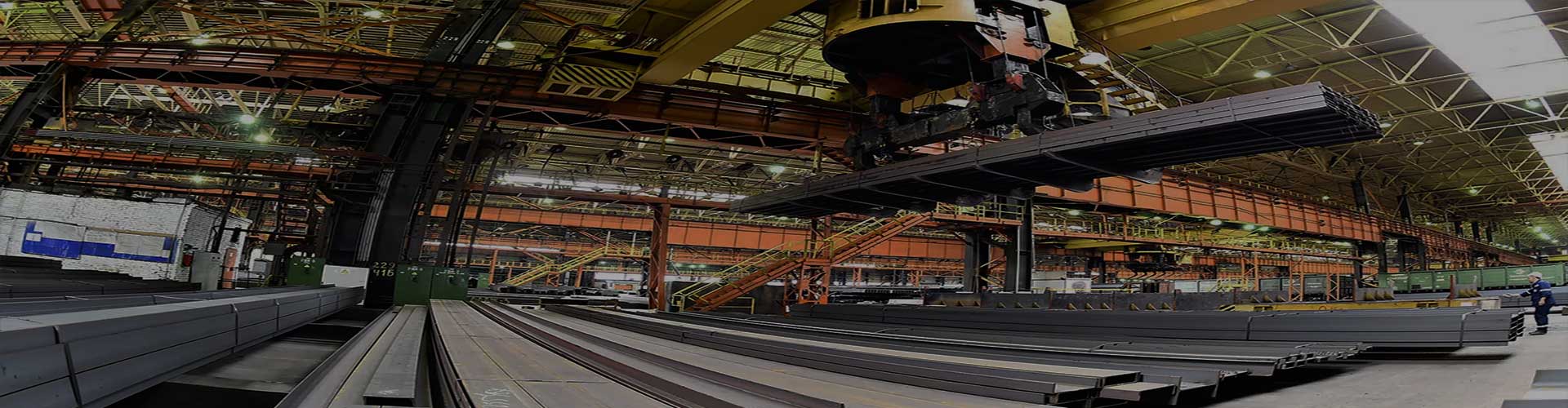
Walking Beam Reheating Furnace
Walking Beam Reheating Furnace
- The walking beam reheating furnace is a crucial component of the steelmaking process and is designed to efficiently and effectively heat steel slabs or billets. Some of the key features of a walking beam reheating furnace include:
- Walking Beam Mechanism: The furnace is equipped with a walking beam mechanism that moves the steel slabs or billets through the furnace on a series of rollers. This mechanism ensures that the steel is heated evenly and consistently throughout the furnace.
- High-Temperature Capacity: The furnace is designed to operate at high temperatures, typically between 1,100°C and 1,300°C. This allows the furnace to quickly and efficiently heat the steel to the desired temperature for rolling or forging.
- Precise Temperature Control: The furnace is equipped with advanced temperature control systems that allow for precise temperature control throughout the furnace. This ensures that the steel is heated to the exact temperature required for the specific steel product being produced.
- Fuel Efficiency: The furnace is designed to be fuel-efficient, using a variety of fuel sources such as natural gas, oil, or coal. This helps to reduce the operating costs of the furnace and makes it more environmentally friendly.
- Low Emissions: The furnace is designed to minimize emissions and is equipped with advanced pollution control systems that capture and treat any emissions produced during the heating process.
- Overall, the walking beam reheating furnace is a critical component of the steelmaking process, helping to ensure that steel is heated to the exact temperature required for the specific steel product being produced.
Description
A walking beam reheating furnace is a type of furnace used in the steel industry to heat steel slabs or billets to a specific temperature prior to rolling or forging. The furnace consists of a series of refractory-lined chambers that are heated using burners or gas-fired heating elements.
The walking beam furnace gets its name from the mechanism used to move the steel through the furnace. The furnace has a series of beams that extend across the chambers, with each beam supporting a set of rollers. The steel slabs or billets are loaded onto the rollers at one end of the furnace and are then moved through the furnace on the beams, with the rollers turning to keep the steel moving.
As the steel moves through the furnace, it is exposed to the high temperatures and is heated to the desired temperature for further processing. The walking beam design of the furnace allows for precise control of the heating process, as the steel moves through the furnace at a controlled speed and is exposed to a consistent temperature for a specific amount of time.
Overall, the walking beam reheating furnace is an important tool in the steel industry, helping to ensure that steel is heated to the correct temperature for further processing and ultimately producing high-quality steel products.
Walking Beam Reheating Furnace: Working principle
The working principle of a walking beam reheating furnace is relatively simple. It is a continuous heating furnace that is used to heat steel slabs or billets to a specific temperature prior to rolling or forging. The furnace is designed to operate at high temperatures, typically between 1,100°C and 1,300°C.
The working principle of a walking beam reheating furnace involves the following steps:
- Loading: The steel slabs or billets are loaded onto the rollers at the inlet end of the furnace.
- Heating: The burners or heating elements in the furnace are activated, heating the refractory-lined chambers. As the steel moves through the furnace on the rollers, it is exposed to the high temperature and is heated to the desired temperature for further processing.
- Movement: The walking beam mechanism moves the steel slabs or billets through the furnace at a controlled speed, ensuring that the steel is exposed to a consistent temperature for a specific amount of time.
- Unloading: Once the steel has been heated to the desired temperature, it is unloaded from the furnace at the outlet end using a transfer table or roller table.
The walking beam mechanism in the furnace consists of a series of beams that extend across the chambers, with each beam supporting a set of rollers. The steel slabs or billets are loaded onto the rollers at one end of the furnace and are then moved through the furnace on the beams, with the rollers turning to keep the steel moving. As the steel moves through the furnace, it is exposed to the high temperatures and is heated to the desired temperature for further processing.
The Characteristics
Some of the key characteristics of a walking beam reheating furnace are:
- High Efficiency: The walking beam reheating furnace is designed to operate continuously, which makes it highly efficient. The furnace can heat a large number of steel slabs or billets in a short amount of time, which increases productivity.
- Precise Temperature Control: The advanced temperature control systems in the furnace allow for precise temperature control throughout the furnace. This ensures that the steel is heated to the exact temperature required for the specific steel product being produced, resulting in consistent quality.
- Even Heating: The walking beam mechanism in the furnace ensures that the steel is heated evenly and consistently throughout the furnace. This results in a high-quality finished product.
- Reduced Energy Consumption: The furnace is designed to minimize energy consumption by using high-efficiency burners or gas-fired heating elements. This results in lower energy costs and reduced environmental impact.
- Improved Safety: The walking beam mechanism in the furnace eliminates the need for manual handling of the steel slabs or billets, which improves safety for workers and reduces the risk of accidents.
The advantages of a walking beam reheating furnace include high efficiency, precise temperature control, even heating, reduced energy consumption, and improved safety. It is a popular choice for steel producers looking to increase productivity and produce high-quality steel products.